A TRUSTED PARTNER TO THE POWER PLANT WATER MANAGEMENT
CHALLENGES IN THE POWER INDUSTRY
The world becomes more power-hungry every day. Demand for electricity keeps growing, and new power generation plants are constructed under increasingly demanding conditions, often in water-stressed locations. New plants are also subject to high regulatory pressure and water-efficiency standards. It is now imperative to find solutions to reduce water consumption and maximize the reuse of water to protect valuable resources. Electrical power generation requires lots of water to remove heat resulting from the energy transfer in thermoelectric plants.
In every power plant in the world, steam from water is the driving force. The quality is important to ensure efficient and reliable operation of the power plant equipment and to protect important and expensive assets.
MEMTIK ultrafiltration (UF) tehcnology is developed to meet the challenges in the power generation industry. This is because of the importance of the pretreatment unit in the reverse osmosis (RO) membrane process for demineralized process water to feed the boiler and cooling water recycling. Those challenges are compounded by the need to deal with the more and more complicated contaminants found in raw water. Water losses must be minimized during processing while maximizing water recycling. These requirements are driven by the increasing awareness of water scarcity and on the subsequent regulations for water conservation and discharge.
The cooling water condenses the vapor out of the turbine. Because of the chemical dosing in the process, the water is exposed to the atmosphere allowing dirt and microorganisms to enter. The cooling water recycling has to face the following challenges:
Scaling
Dirt scale
Corrosion
Microbial slime
Scaling: due to constant evaporation of the circulating water evaporation in the process of cooling, the salt concentration increases. When this level exceeds the solubility of some salt, precipitation will occur. Calcium carbonate, calcium phosphate and silicate scale are common byproducts in the process. The scale greatly reduces the efficiency of heat exchange. The heat transfer coefficient decreases 20% where the scale of thickness is 0.6 mm.
Dirt scale: the dirt scale consists of organics, microbial colonies, secretions, and dust. The scale has a soft texture. It decreases the heat transfer efficiency and causes corrosions under deposit, which shortens the service life of the equipment.
Corrosion: the corrosion caused by circulating water is mainly electrochemical corrosion. Contributing factors are equipment manufacturing defects, oxygen in the water, corrosive ions (Cl-, Fe2+, Cu2+), and microbial mucus slime. If the corrosion is not controlled, the heat exchanger and pipeline will be damaged in a short period.
Microbial slime: the circulating water is suitable for the growth and reproduction of microorganisms. This is because of the sufficient dissolved oxygen, proper temperature and eutrophic conditions. Without timely control, this will rapidly leads to the deterioration of water quality and mucilaginous deposition. The heat transfer efficiency will decrease substantially and increase the equipment corrosion. To prevent this, microorganisms in the circulation water treatment must be controlled. Treatment and recycling of the cooling water can significantly save the water resource and reduce the environmental burden. Pretreatment and demineralization is an effective process.
The Memtik UF membranes are the ideal solution to control suspended contaminants and microbiology in the water and protect further downstream demineralization process running with safety, reliability and lower maintenance.
Key Benefit for Boiler Feed Water Treatment:
Ensure proper and efficient operation of steam generation system
Improve operation & steam purity
Improve condensate corrosion control
Reduce fuel costs through lower heat loss and increased boiler cycles
Reduce boiler system chemical treatment costs
Reduce risk
Reduce external treatment costs; particularly if previously using cold or hot lime softening, ion exchange and / or re-generable DI
Remove / reduce hazardous acid and caustic chemicals
Some Membrane Usage Example:
MF – bacteria spore removal from skim milk, whey and WPC
MF and UF – protein fractionation
MF – delipidization of whey
MF – chemical recovery
UF – concentration and fractionation of proteins in milk
UF – brine clarification
NF – demineralization of UF permeate
NF – demineralization of whey
NF – milk electrolytes
RO – water removal from whey and other streams
Our Capabilty & Strength
Power Generation
By employing advanced membrane treatment technologies and related services, Memtik helps power generators achieve their specific water quality goals, while also improving efficiency and reducing waste.
From high pressure boiler feed to systems that treat cooling tower make-up, Memtik offers a wide range of equipment and technology solutions that help power generators ensure consistent, cost-effective and reliable water quality. Our systems are supported by a team of highly skilled engineers and technicians, available 24/7/365.
With integrated solutions, comprehensive support services, Memtik is dedicated to help our customers conserve, protect and manage their water resources today, and into the future.
Common Applications
Boiler Water
Condensate Polishing
Cooling Tower Water
Pre-treatment
Wastewater
Recycle/Reuse
Our Products and Services Include
Media Filtration
MF/UF
NF/RO
Demineralizers
Condensate Polishing
TOC Reduction Systems
Electrodeionization
Membrane Degassifiers
B31.1 Piping Design & Fabrication
Process Control/Automation Solutions
Remote Monitoring
New Installations
Upgrades & Retrofits
Process Evaluation & Optimization Services
Aftermarket Parts
Process Water
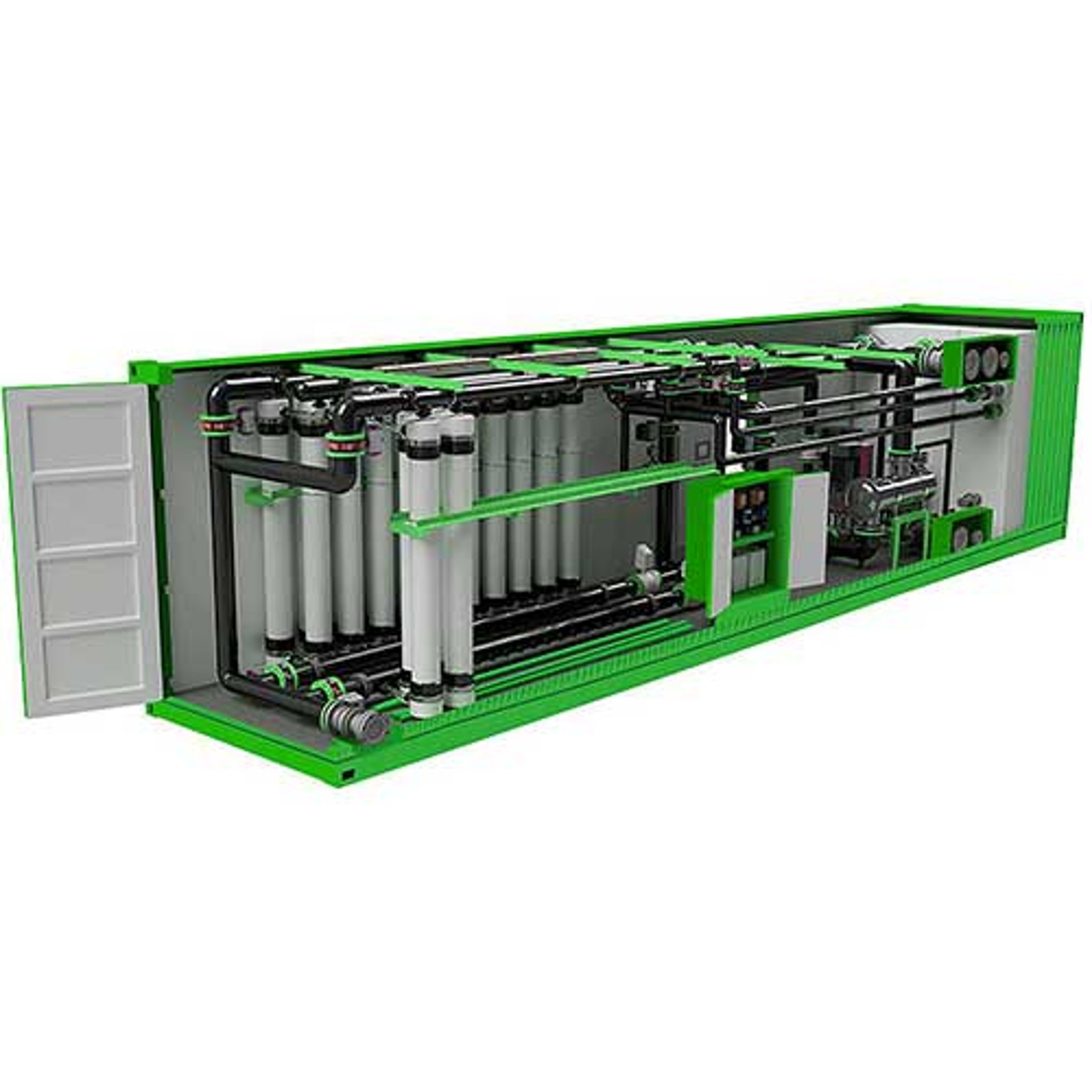
In-Process Filtration
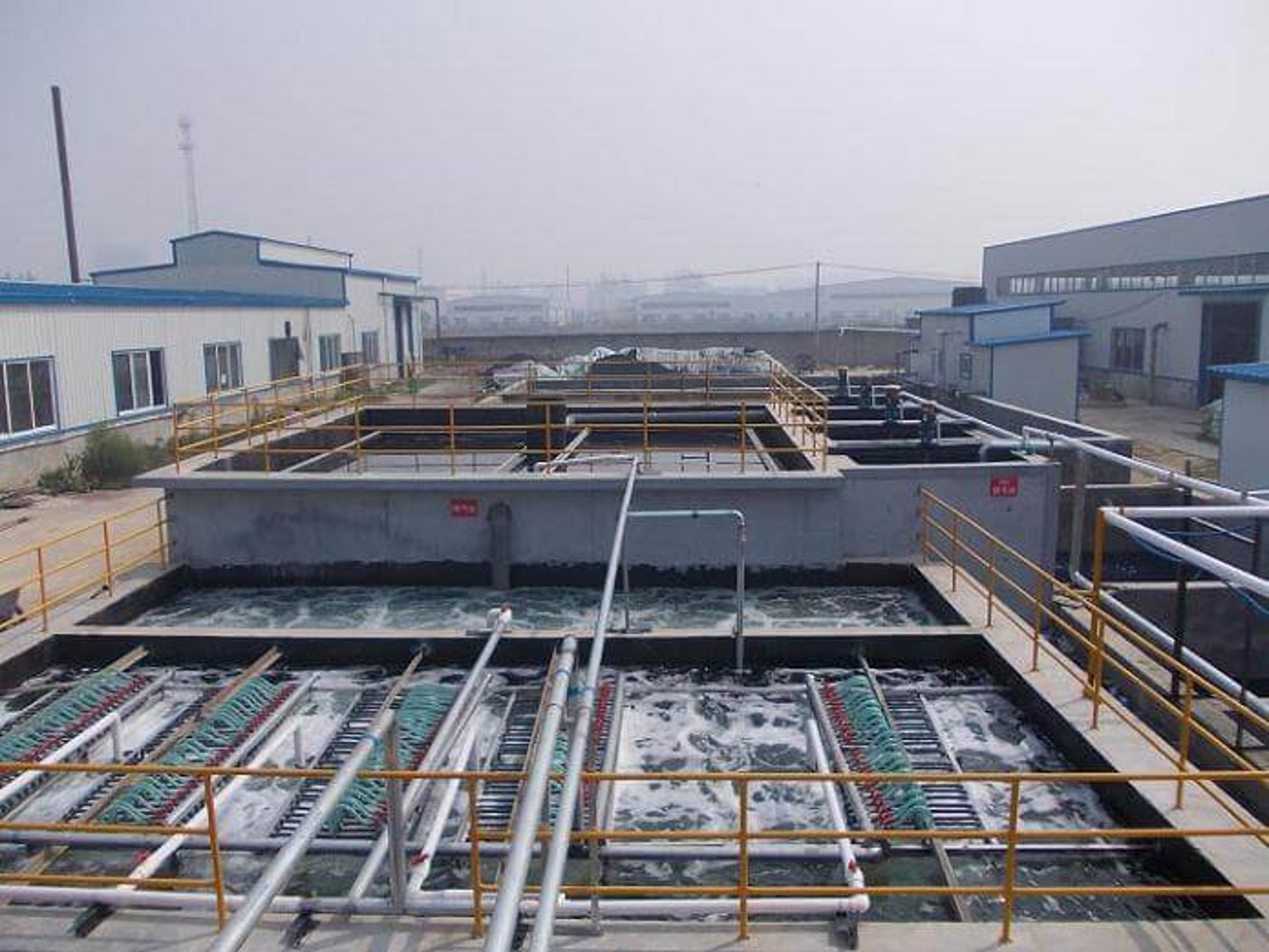