A TRUSTED PARTNER TO THE OIL & GAS INDUSTRY
Membrane Technology for Chemicals
The chemical industry is very diverse and uses all of the major process technologies. However, the demand for higher product quality, shorter paybacks and reduced operating costs is increasing. As product separation becomes more complex the use of membrane technology is increasing. This is particularly the case in the fine chemical industry where the membranes are used in a variety of applications for example in the concentration and desalting of dyestuffs and optical brighteners.
PCI tubular membrane technology is developing to meet the demands of the chemical industry and new membranes are being produced which can operate in more extreme conditions such as high temperature, high/low pH and are more resistant to solvents.
New applications for tubular membrane are continually being found where they offer significant advantages over more conventional technologies and key applications are:
Chemical processors today are faced with mounting pressure to reduce wastewater volumes and treatment costs. While environmental regulations and “green” politics create a demand for companies to cut effluent volumes, economics also plays a major role. Discharge costs for wastewater are rising, as are charges for disposal and landfill of sludge generated from traditional wastewater treatment systems.
Fresh water prices continue to increase as demand increases and availability drops.
In addition, some effluent constituents, if recovered, can be quite valuable. For these reasons, discharging process wastewater can be literally like throwing money down the drain, especially when there are convenient alternatives.
One of the most effective approaches to dealing with some or all of these issues is crossflow membrane filtration technology. The technology can achieve a reduction in the volume of wastewater by a factor of typically 5-10 times and sometimes much higher. It offers potential savings on effluent charges, produces a stream of clean water, solvent or process fluid that can often be reused within the facility, and frequently yields retained waste material, uncontaminated by waste treatment chemicals, which can be reused in the production process or processed further to extract valuable raw materials.
Thus, it is often possible to achieve a true “closed-loop” or “zero discharge” plant. Payback on the capital cost of the membrane installation can be less than two years depending upon the application.
Key Water Applications:
Recovery and reuse of water from waste streams
Biomass separation
Textile and dye effluent treatment
Pulp and paper effluent treatment
Landfill leachate concentration
CIP solution recycle
Pesticide and herbicide removal
Food industry effluents
Oily wastewater treatment
Recovery of laundry water/detergent waste
Key In-Process Applications:
Lignosulphonate recovery and fractionation
Silica sols concentration
Dyestuff and pigment concentration, purification and desalting
Optical brightener purification & concentration
Recovery of cleaning chemicals (Reco-Cip)
Surfactant desalting.
Some Membrane Usage Example:
MF – chemical recovery
UF – brine clarification
NF – demineralization of UF permeate
Our Capabilty & Strength
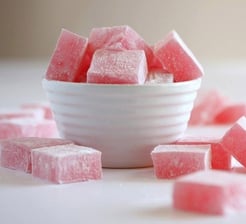

Sweetener
A sweetener is a food additive that provides a sweet taste like that of sugar while containing significantly less food energy. Some sugar substitutes are produced by nature, and others produced synthetically. Those that are not produced by nature are, in general, called artificial sweeteners.
Removal of haze and color from sugar syrup, the concentration of sugar water, can both be accomplished via ceramic membrane filtration processes.
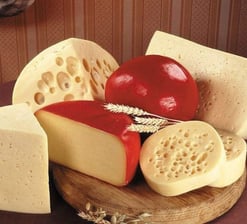

CHEESE, MILK, WHEY AND FOOD PROTEIN
Concentrated milk proteins (MPCs) and isolated milk proteins (MPIs) are produced by ceramic membrane filtration system and their dairy proteins are separated from fresh skim milk. They combine rich calcium with good thermal stability and refreshing mouthfeel. They are rich in casein and whey protein in the same proportions as skim milk.
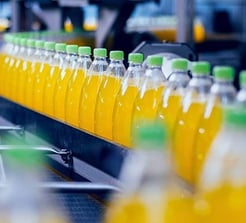

In the fruit juice industry, fruit juice membrane technology is used mainly to clarify the juice by means of ceramic ultrafiltration and microfiltration and to concentrate it by means of nanofiltration and reverse osmosis.
Membrane fouling is a critical issue and inhibits the broader application of membranes in the fruit production industry. Pectin and its derivatives form a gel-like structure over the membrane surface, thereby reducing the permeate flux. In order to degrade pectin, the raw juice is usually subjected to an enzymatic treatment with pectinase, which hydrolyzes pectin and causes its protein complexes to flocculate. The resulting juice has reduced viscosity and much lower pectin content, which is advantageous in the subsequent filtration processes.
Membrane crossflow filtration is widely used in wine membrane filter system for wine filtration, especially as the red wine filter. It can also be used for cross flow filtration beer. Now, the membrane crossflow filtration technology potential for energy-efficiency has made it a viable technique for the clarification of wine and other beverages.
Membrane crossflow filtration is one of the environmentally-friendly wine filtration systems. During the filtration, no filter aid is used. In one step, crossflow filtration clarifies the wine, giving it a clear appearance and making the wine microbiologically stable. So it has very strong advantages in simplifying the steps before bottling and reducing or eliminating the need for some consumables.
Process Water
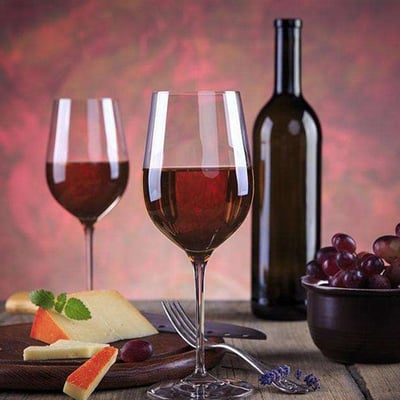
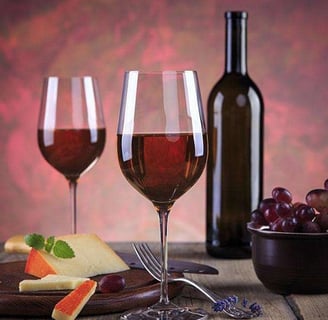
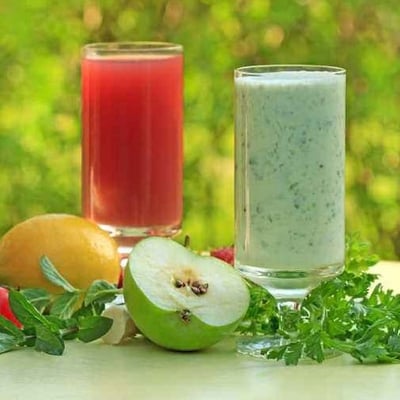
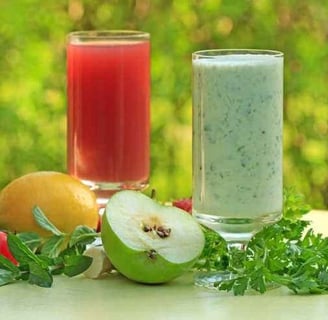
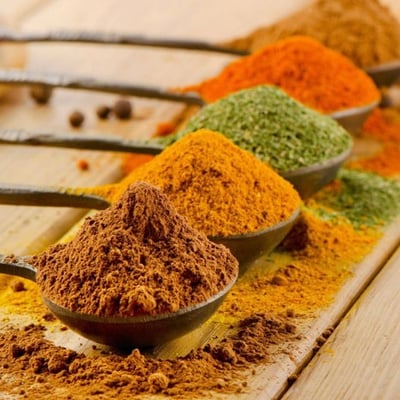
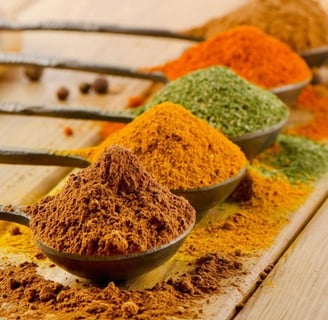
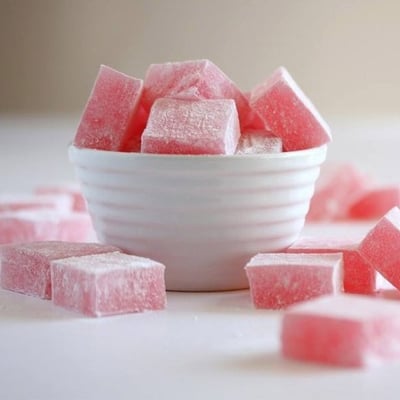
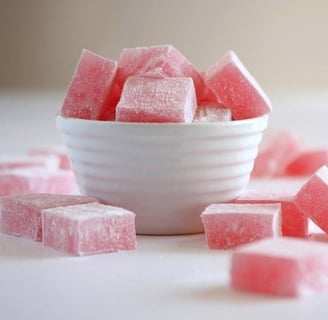
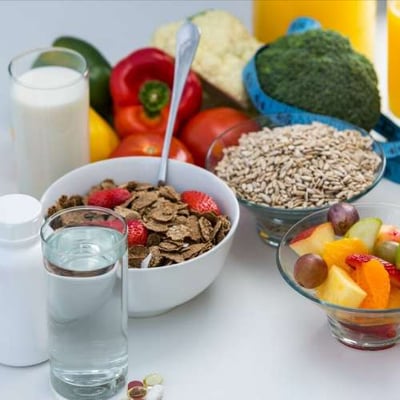
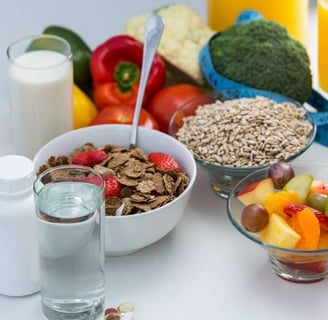
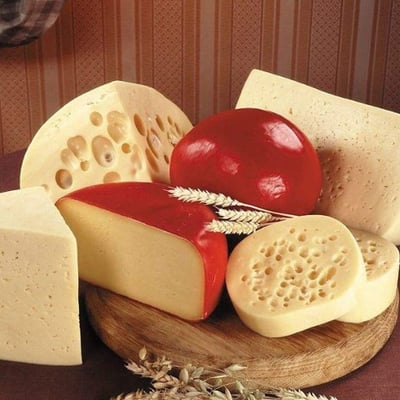
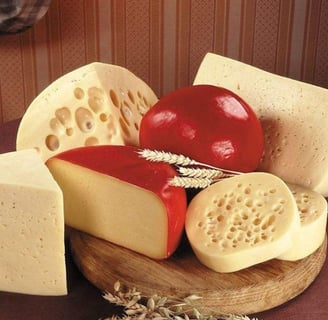
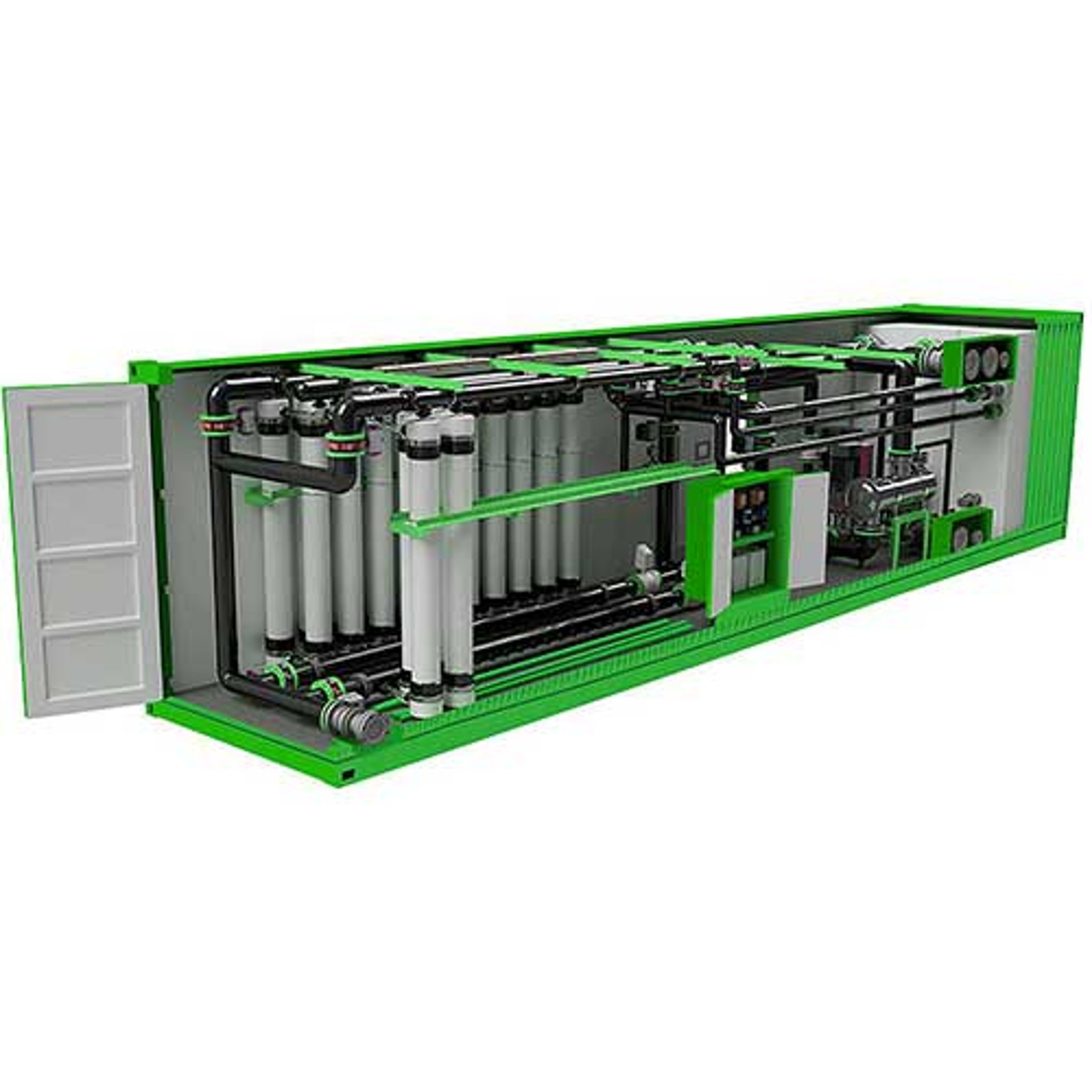
In-Process Filtration
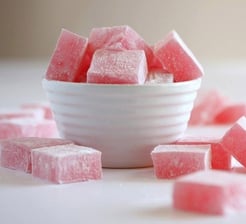

Sweetener
A sweetener is a food additive that provides a sweet taste like that of sugar while containing significantly less food energy. Some sugar substitutes are produced by nature, and others produced synthetically. Those that are not produced by nature are, in general, called artificial sweeteners.
Removal of haze and color from sugar syrup, the concentration of sugar water, can both be accomplished via ceramic membrane filtration processes.
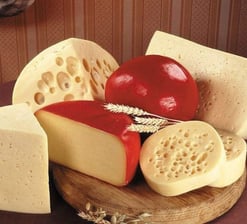

CHEESE, MILK, WHEY AND FOOD PROTEIN
Concentrated milk proteins (MPCs) and isolated milk proteins (MPIs) are produced by ceramic membrane filtration system and their dairy proteins are separated from fresh skim milk. They combine rich calcium with good thermal stability and refreshing mouthfeel. They are rich in casein and whey protein in the same proportions as skim milk.
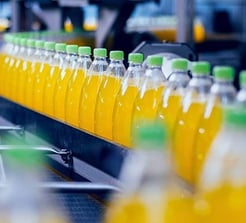

In the fruit juice industry, fruit juice membrane technology is used mainly to clarify the juice by means of ceramic ultrafiltration and microfiltration and to concentrate it by means of nanofiltration and reverse osmosis.
Membrane fouling is a critical issue and inhibits the broader application of membranes in the fruit production industry. Pectin and its derivatives form a gel-like structure over the membrane surface, thereby reducing the permeate flux. In order to degrade pectin, the raw juice is usually subjected to an enzymatic treatment with pectinase, which hydrolyzes pectin and causes its protein complexes to flocculate. The resulting juice has reduced viscosity and much lower pectin content, which is advantageous in the subsequent filtration processes.
Membrane crossflow filtration is widely used in wine membrane filter system for wine filtration, especially as the red wine filter. It can also be used for cross flow filtration beer. Now, the membrane crossflow filtration technology potential for energy-efficiency has made it a viable technique for the clarification of wine and other beverages.
Membrane crossflow filtration is one of the environmentally-friendly wine filtration systems. During the filtration, no filter aid is used. In one step, crossflow filtration clarifies the wine, giving it a clear appearance and making the wine microbiologically stable. So it has very strong advantages in simplifying the steps before bottling and reducing or eliminating the need for some consumables.
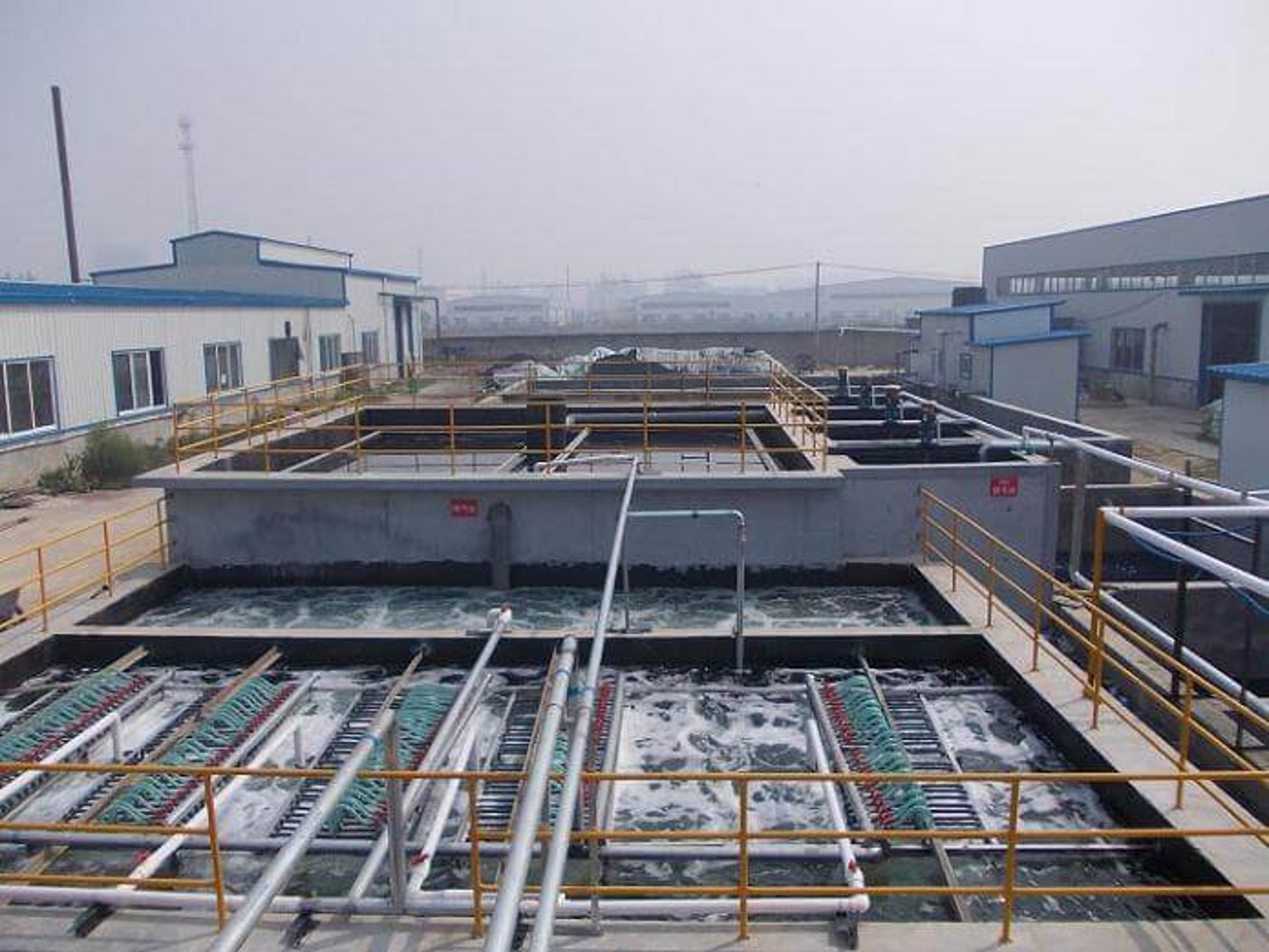
Wastewater Treatment
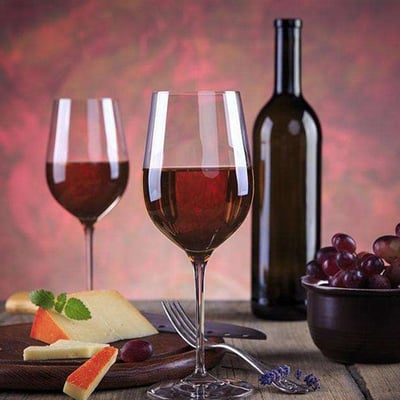
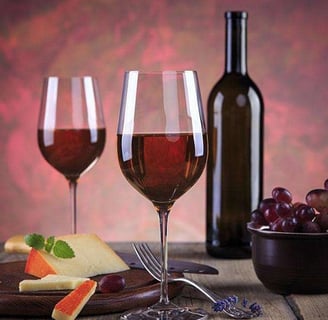
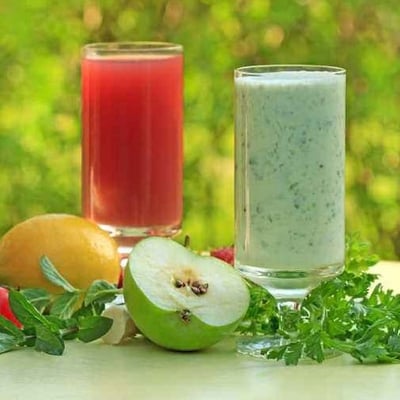
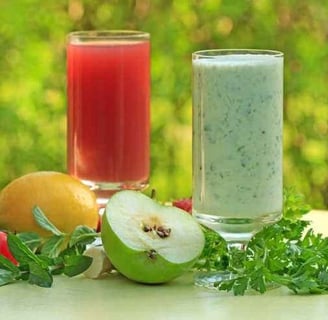
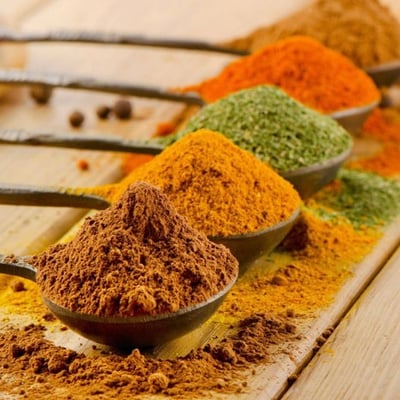
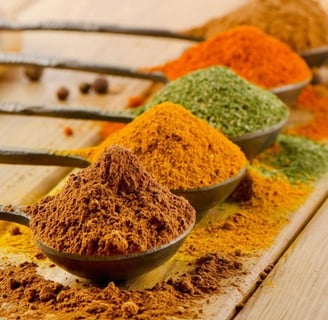
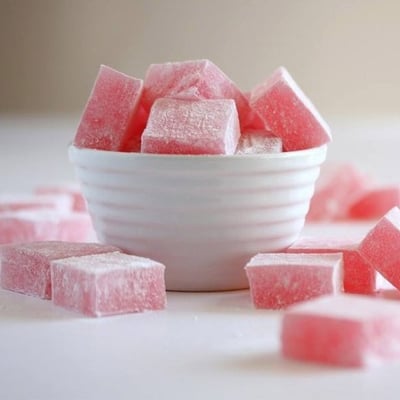
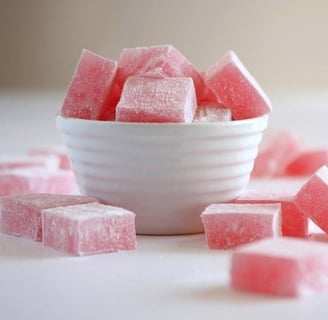
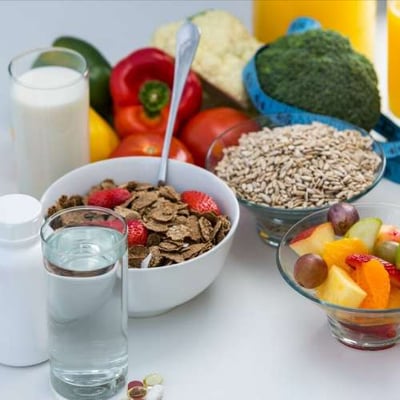
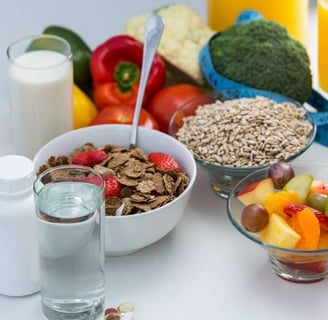
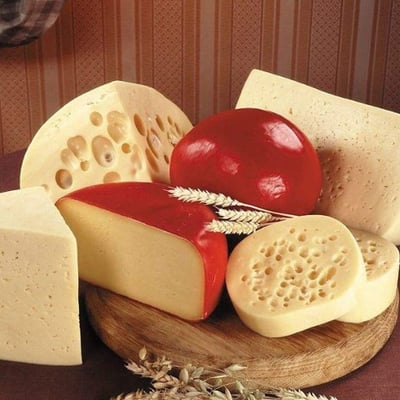
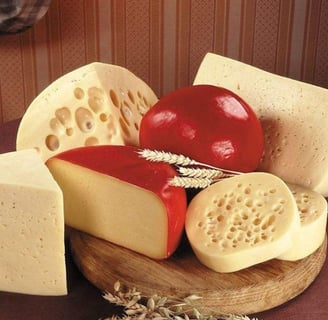