A TRUSTED PARTNER TO THE OIL & GAS INDUSTRY
Renewal Energy Solutions
During the last three decades, climate change, and its effects, has gained world-wide attention. Most leading nations have agreed that global CO2 emissions must be reduced and alternatives to harmful fossil fuels need to be found. Scientists at research centers and universities are working to develop sustainable energy solutions to optimize current energy technologies. As a result, many sustainable energy technologies have been developed.
To date, solar and wind energies have proven to be the most common sustainable solutions. Due to the development of new methodologies, the usage of biofuels is increasing. This new technology allows the conversion of biomass into fuels that can generate energy. The most recognized of these include bioethanol, biodiesel and biogas.
Biofuels are classified in four different generations. Each generation refers to the biomass feedstocks. A feedstock is defined as any renewable, biological material that can be used directly as a fuel or converted to another form of fuel or energy product. Benefits from biofuels include economic, environmental, storage and waste management.
First-generation biofuels are produced from biomass feedstocks that can be used as food or waste such as pure oil, sugar, starch or the waste of frying oil. Examples include bioethanol, pure vegetable oil, biodiesel and biogas. Fermentation and transesterification are used as conversion processes during the production of these biofuels.
Second-generation biofuels are produced from feedstocks that are not usable as food such as lignocellulosic material. These types of biofuel are bioethanol, synthetic biofuels and biogas. Fermentation, gasification and fast-pyrolysis are used as conversation processes during this production.
Third-generation biofuels are a direct enhancement of the second generation. For example, focus is placed on the lignocellulosic material that renders the highest conversation of biofuels, such as algae.
In the fourth generation, CO2 emissions are captured and stored to use as feedstock to plants that are intended to produce biofuels.
Filtration can be used in general to:
remove polyethylene and other plastics from animal oil
remove sterols
remove glucosides
pre-treat oil to make it clean enough to convert into biodiesel
bleach animal oil
remove sulphur from animal oil
remove proteins from animal oil
remove absorbents such as silica
remove phosphorus
remove mono-glyceride
remove strains
remove waxes and gums
wash, dry and purify end products such as biodiesel and glycerin
remove polycyclic aromatic hydrocarbons (PAHs)
Key Water Applications:
Recovery and reuse of water from waste streams
Biomass separation
Textile and dye effluent treatment
Pulp and paper effluent treatment
Landfill leachate concentration
CIP solution recycle
Pesticide and herbicide removal
Food industry effluents
Oily wastewater treatment
Recovery of laundry water/detergent waste
Key In-Process Applications:
Lignosulphonate recovery and fractionation
Silica sols concentration
Dyestuff and pigment concentration, purification and desalting
Optical brightener purification & concentration
Recovery of cleaning chemicals (Reco-Cip)
Surfactant desalting.
Some Membrane Usage Example:
MF – chemical recovery
UF – brine clarification
NF – demineralization of UF permeate
Our Capabilty & Strength
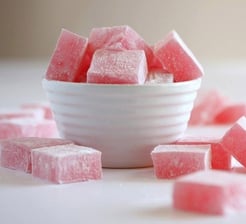

Sweetener
A sweetener is a food additive that provides a sweet taste like that of sugar while containing significantly less food energy. Some sugar substitutes are produced by nature, and others produced synthetically. Those that are not produced by nature are, in general, called artificial sweeteners.
Removal of haze and color from sugar syrup, the concentration of sugar water, can both be accomplished via ceramic membrane filtration processes.
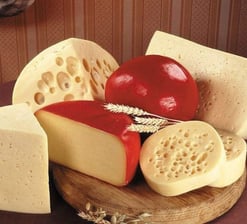

CHEESE, MILK, WHEY AND FOOD PROTEIN
Concentrated milk proteins (MPCs) and isolated milk proteins (MPIs) are produced by ceramic membrane filtration system and their dairy proteins are separated from fresh skim milk. They combine rich calcium with good thermal stability and refreshing mouthfeel. They are rich in casein and whey protein in the same proportions as skim milk.
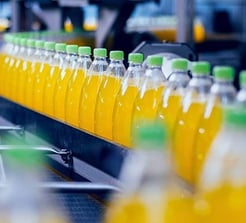

In the fruit juice industry, fruit juice membrane technology is used mainly to clarify the juice by means of ceramic ultrafiltration and microfiltration and to concentrate it by means of nanofiltration and reverse osmosis.
Membrane fouling is a critical issue and inhibits the broader application of membranes in the fruit production industry. Pectin and its derivatives form a gel-like structure over the membrane surface, thereby reducing the permeate flux. In order to degrade pectin, the raw juice is usually subjected to an enzymatic treatment with pectinase, which hydrolyzes pectin and causes its protein complexes to flocculate. The resulting juice has reduced viscosity and much lower pectin content, which is advantageous in the subsequent filtration processes.
Membrane crossflow filtration is widely used in wine membrane filter system for wine filtration, especially as the red wine filter. It can also be used for cross flow filtration beer. Now, the membrane crossflow filtration technology potential for energy-efficiency has made it a viable technique for the clarification of wine and other beverages.
Membrane crossflow filtration is one of the environmentally-friendly wine filtration systems. During the filtration, no filter aid is used. In one step, crossflow filtration clarifies the wine, giving it a clear appearance and making the wine microbiologically stable. So it has very strong advantages in simplifying the steps before bottling and reducing or eliminating the need for some consumables.
Process Water
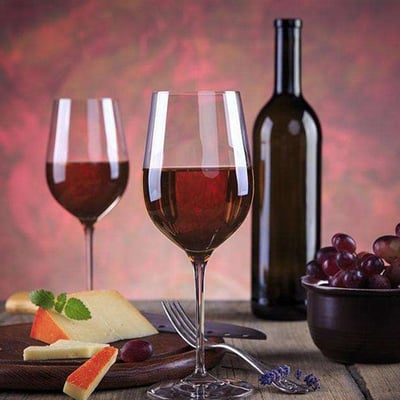
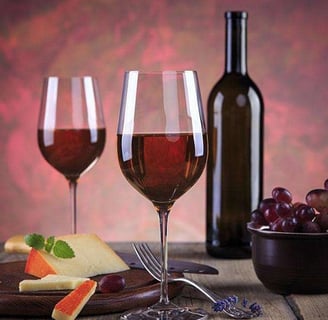
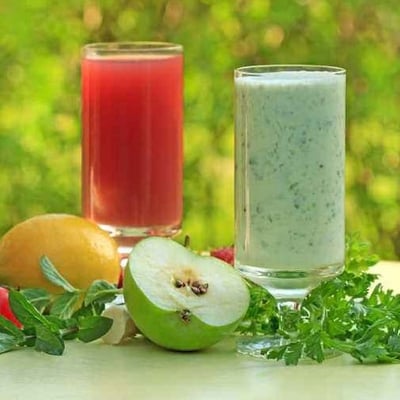
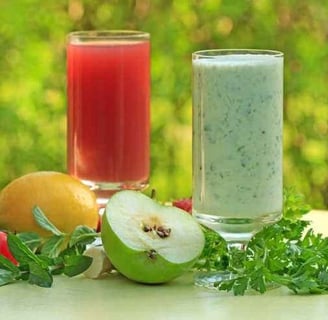
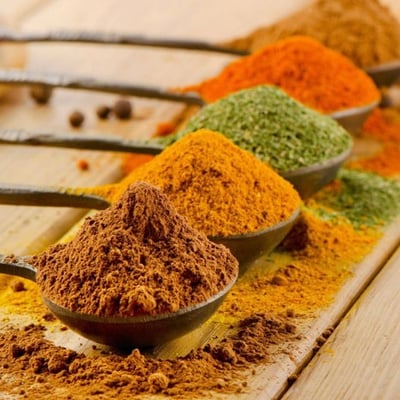
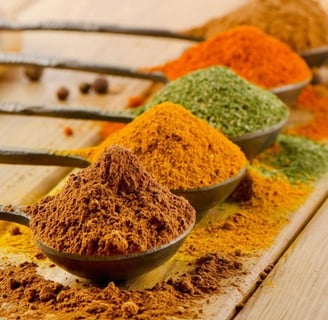
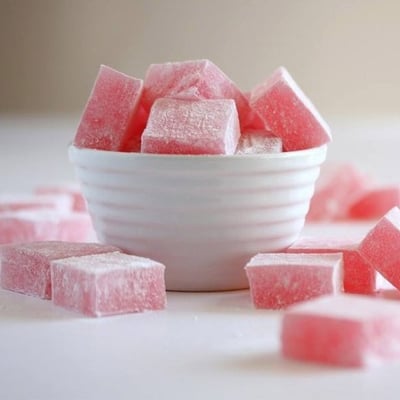
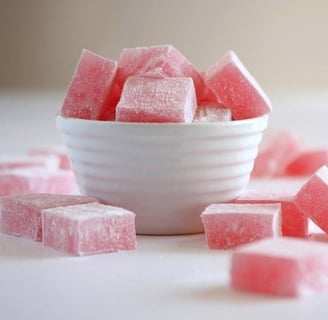
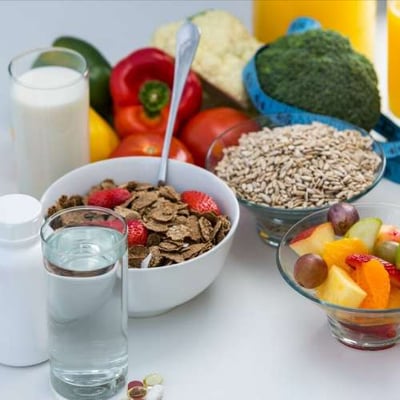
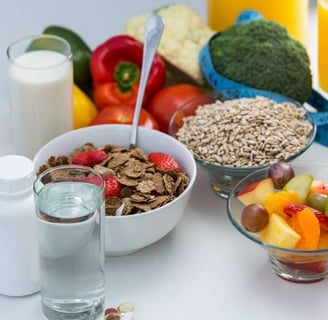
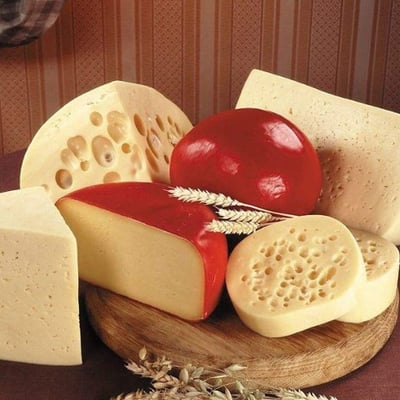
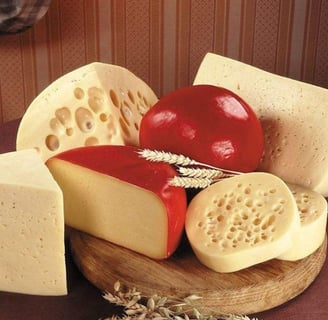
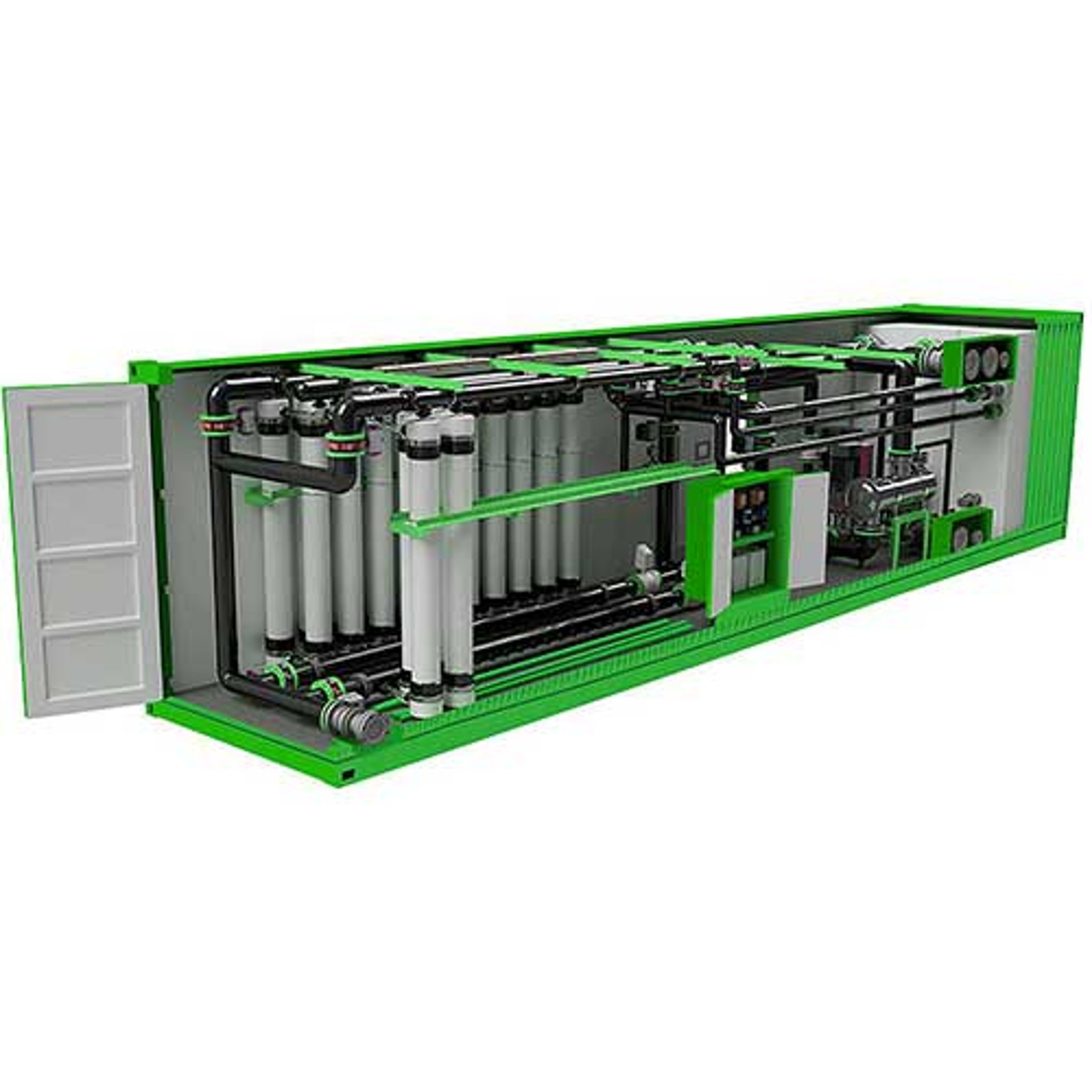
In-Process Filtration
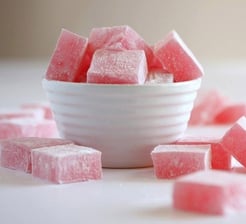

Sweetener
A sweetener is a food additive that provides a sweet taste like that of sugar while containing significantly less food energy. Some sugar substitutes are produced by nature, and others produced synthetically. Those that are not produced by nature are, in general, called artificial sweeteners.
Removal of haze and color from sugar syrup, the concentration of sugar water, can both be accomplished via ceramic membrane filtration processes.
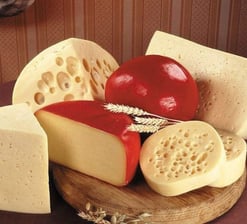

CHEESE, MILK, WHEY AND FOOD PROTEIN
Concentrated milk proteins (MPCs) and isolated milk proteins (MPIs) are produced by ceramic membrane filtration system and their dairy proteins are separated from fresh skim milk. They combine rich calcium with good thermal stability and refreshing mouthfeel. They are rich in casein and whey protein in the same proportions as skim milk.
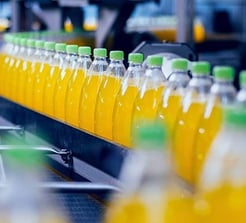

In the fruit juice industry, fruit juice membrane technology is used mainly to clarify the juice by means of ceramic ultrafiltration and microfiltration and to concentrate it by means of nanofiltration and reverse osmosis.
Membrane fouling is a critical issue and inhibits the broader application of membranes in the fruit production industry. Pectin and its derivatives form a gel-like structure over the membrane surface, thereby reducing the permeate flux. In order to degrade pectin, the raw juice is usually subjected to an enzymatic treatment with pectinase, which hydrolyzes pectin and causes its protein complexes to flocculate. The resulting juice has reduced viscosity and much lower pectin content, which is advantageous in the subsequent filtration processes.
Membrane crossflow filtration is widely used in wine membrane filter system for wine filtration, especially as the red wine filter. It can also be used for cross flow filtration beer. Now, the membrane crossflow filtration technology potential for energy-efficiency has made it a viable technique for the clarification of wine and other beverages.
Membrane crossflow filtration is one of the environmentally-friendly wine filtration systems. During the filtration, no filter aid is used. In one step, crossflow filtration clarifies the wine, giving it a clear appearance and making the wine microbiologically stable. So it has very strong advantages in simplifying the steps before bottling and reducing or eliminating the need for some consumables.
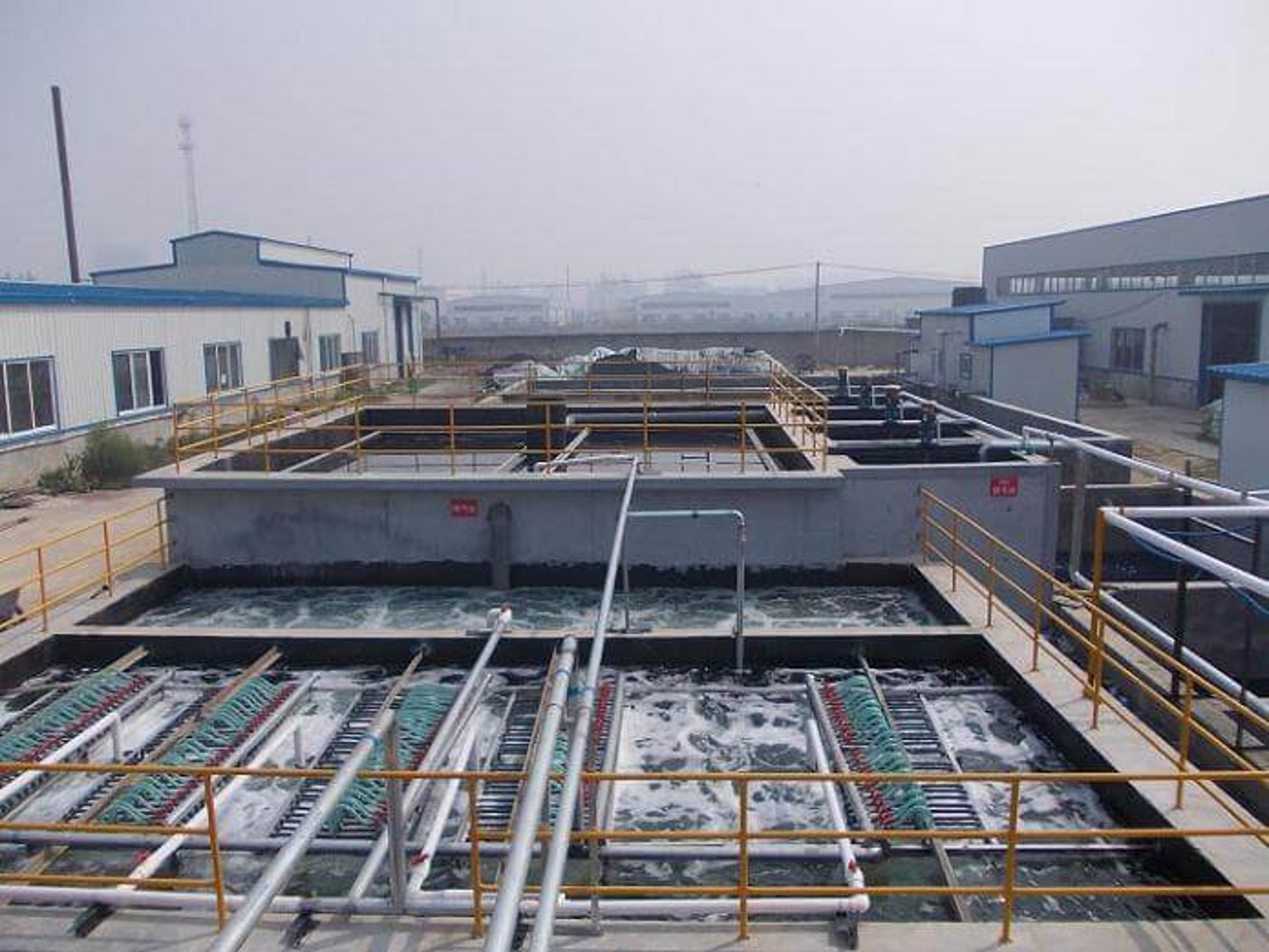
Wastewater Treatment
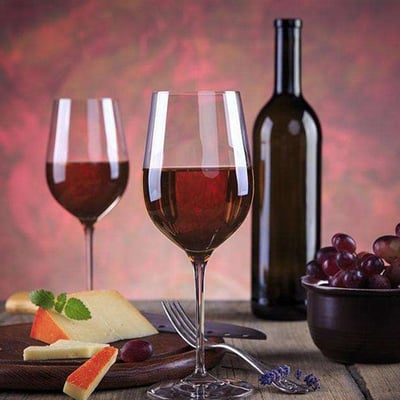
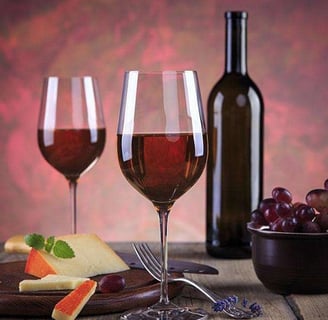
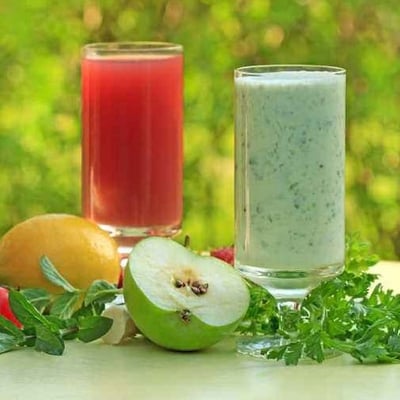
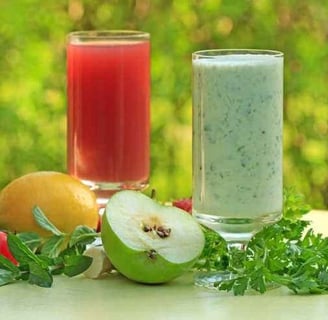
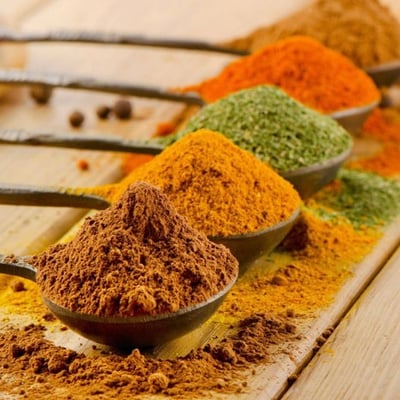
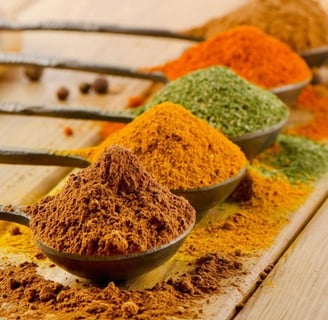
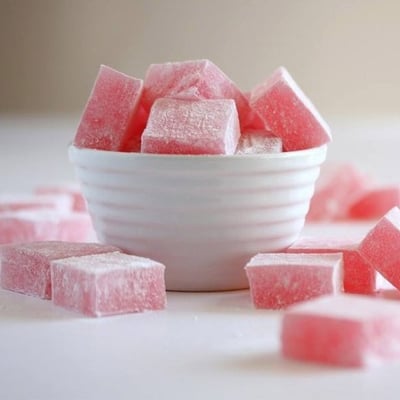
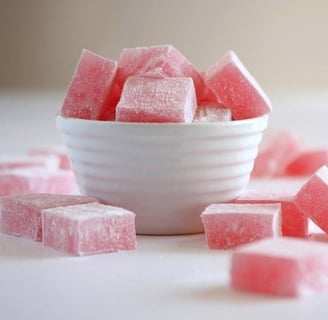
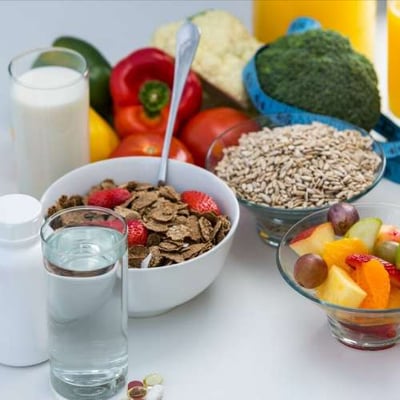
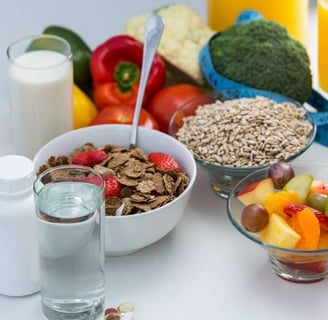
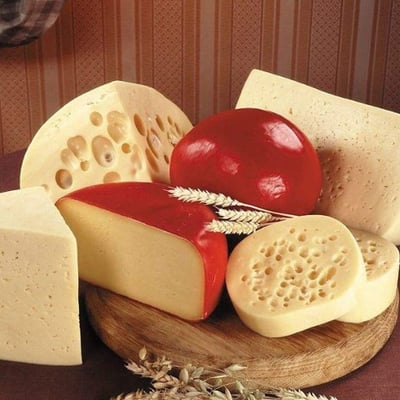
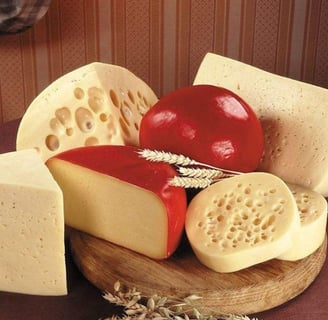